By niuelec | 03 April 2025 | 0 Comments
From Design to Delivery: Inside a Leading Copper Wire Clamp Manufacturer's Production Process
Understanding the intricate processes behind manufacturing essential components like copper wire clamp can provide valuable insights for buyers seeking reliable and high-quality suppliers. A behind-the-scenes look at a leading copper wire clamp manufacturer reveals the dedication to precision, quality control, and innovation that goes into each product. From the initial design phase to the final delivery, every step is carefully orchestrated to ensure optimal performance and durability. This guide will take you on a journey through the manufacturing process, highlighting the key steps and technologies involved. We'll also explore why global buyers increasingly trust Chinese copper wire clamp manufacturers, and how specialized solutions like transformer braid clamps ensure both durability and conductivity in demanding applications. Gaining this knowledge empowers you to make informed sourcing decisions and build stronger, more reliable supply chains.
Table of contents:
Step-by-Step Manufacturing Insights from a Copper C-Clamp Manufacturer
Why Global Buyers Trust Chinese Copper Wire Clamp Manufacturers
Ensuring Durability and Conductivity with Transformer Braid Clamp Solutions
In conclusion, understanding the production process, the reasons behind the global trust in Chinese manufacturers, and the specific requirements for specialized applications like transformer braid clamps are all critical for making informed sourcing decisions. By partnering with a reputable copper wire clamp manufacturer that prioritizes quality, innovation, and customer satisfaction, you can ensure the reliability and performance of your electrical systems. Take the time to research potential suppliers, ask detailed questions about their manufacturing processes, and request samples to evaluate their quality firsthand. This investment will pay off in the long run by reducing risks and building a stronger, more resilient supply chain.
Table of contents:
Step-by-Step Manufacturing Insights from a Copper C-Clamp Manufacturer
Why Global Buyers Trust Chinese Copper Wire Clamp Manufacturers
Ensuring Durability and Conductivity with Transformer Braid Clamp Solutions
Step-by-Step Manufacturing Insights from a Copper C-Clamp Manufacturer
The production of a copper C-clamp manufacturer typically involves several key stages, each critical to the final product's quality. It begins with design and engineering, where engineers create detailed blueprints and specifications based on customer requirements or existing designs. Next, raw materials, primarily high-quality copper, are carefully selected and inspected to ensure they meet the required standards for conductivity and purity. The manufacturing process then moves to forming and shaping, where the copper is cut, bent, and molded into the desired C-clamp shape using specialized machinery. This is often followed by machining, where precise dimensions and tolerances are achieved through processes like milling and drilling. Surface treatment, such as plating or coating, is then applied to enhance corrosion resistance and improve conductivity. Finally, each clamp undergoes rigorous quality control inspections to ensure it meets all specifications before being packaged and prepared for shipment. This meticulous step-by-step process ensures that every clamp leaving the factory is of the highest quality and ready for its intended application.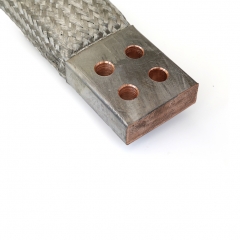
Why Global Buyers Trust Chinese Copper Wire Clamp Manufacturers
The rise of Chinese copper wire clamp manufacturers as trusted suppliers in the global market is driven by several factors. Firstly, significant investments in modern manufacturing technology and infrastructure have enabled Chinese manufacturers to produce high-quality clamps at competitive prices. Secondly, China boasts a large and skilled workforce, providing the necessary expertise to handle complex manufacturing processes. Thirdly, Chinese manufacturers are increasingly focused on meeting international standards and certifications, demonstrating their commitment to quality and reliability. Furthermore, many Chinese manufacturers offer comprehensive OEM/ODM services, allowing global buyers to customize clamps to their specific needs and branding requirements. Finally, the sheer scale of production in China allows for shorter lead times and greater flexibility in meeting fluctuating demand. These factors combined have made Chinese manufacturers a compelling choice for global buyers seeking cost-effective and reliable copper wire clamp solutions.Ensuring Durability and Conductivity with Transformer Braid Clamp Solutions
In specialized applications like transformers, maintaining both durability and conductivity in clamp solutions is paramount. Transformer braid clamps are designed to provide a secure and reliable connection for transformer braids, which are flexible conductors used to carry high currents. These clamps are typically made from high-conductivity copper alloys and are designed to withstand the high temperatures and vibrations associated with transformer operation. To ensure durability, manufacturers often employ robust designs with reinforced structures and corrosion-resistant coatings. Conductivity is maximized by using materials with high electrical conductivity and designing the clamp to provide a large contact area with the transformer braid. Furthermore, specialized testing procedures are used to verify the clamp's performance under extreme conditions. Choosing a manufacturer with expertise in transformer braid clamp solutions is crucial for ensuring the reliability and longevity of your transformer systems. Manufacturers like Niuelec who specialize in braid flexible wire and transformer braids are well-positioned to offer complementary clamping solutions.In conclusion, understanding the production process, the reasons behind the global trust in Chinese manufacturers, and the specific requirements for specialized applications like transformer braid clamps are all critical for making informed sourcing decisions. By partnering with a reputable copper wire clamp manufacturer that prioritizes quality, innovation, and customer satisfaction, you can ensure the reliability and performance of your electrical systems. Take the time to research potential suppliers, ask detailed questions about their manufacturing processes, and request samples to evaluate their quality firsthand. This investment will pay off in the long run by reducing risks and building a stronger, more resilient supply chain.
Leave a Reply
Your email address will not be published.Required fields are marked. *
CATEGORIES